BrightenHiFi
来到Paradigm这处北美最大的音响生产基地,工厂整整走了一天才看完,上千张照片整理起来煞费工夫,从中一一理出头绪,这才更感受到Paradigm喇叭的自制率有多高。
音箱的组件比起插电器材来说,相对少得多,音箱箱体加上单元、分音器、配线与端子,大概就没了,顶多讲讲里面的阻尼物,可是如果我们细细讲究,每一项组件里面又包含许多零件,譬如喇叭有振膜、悬边、弹波、音圈、磁铁、框架等等,假如每一个地方都要自己做,那就是高度垂直整合,Paradigm就是这么讲究,几乎什么东西都自己来,拥有超高的自制率。
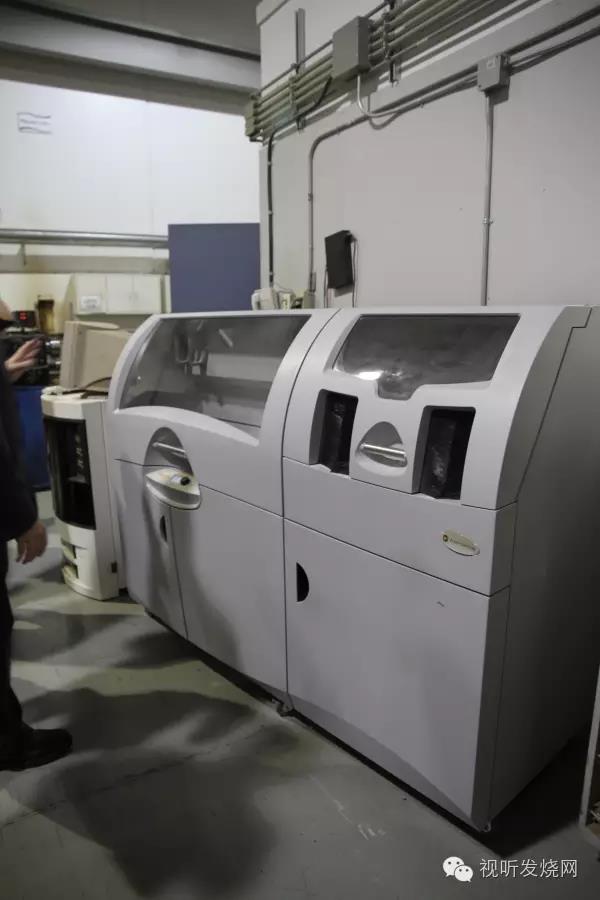 |
这是3D打印机,所有的喇叭框架都可以从这里得到试作品,而且打样的速度很快。 |
Paradigm的设计工程师Oleg Bogdanov告诉我们,为Paradigm几乎尽可能自己制作零件,所以研发部门要密切与生产部门合作。现在Paradigm已经追上了最新的技术,就是使用3D打印机,Oleg说3D打印机是是工程师们的梦想成真,当他们早上画好3D原型图,下午就可以拿到样品,开始测试是否可行,大幅加速了设计的速度。而且不光是单元,连音箱成品、分音器都可以利用3D打印机加速研发的速度。
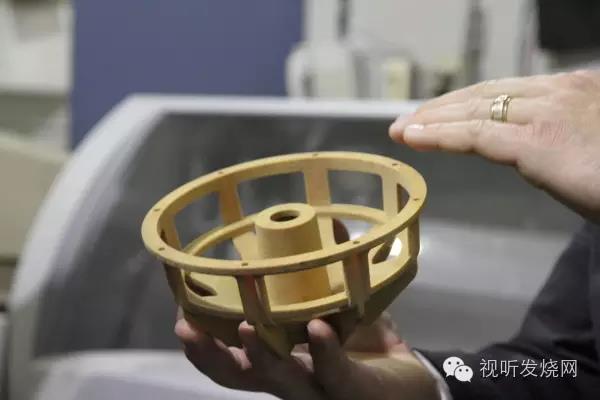 |
3D打印机制作的喇叭框体原型。 |
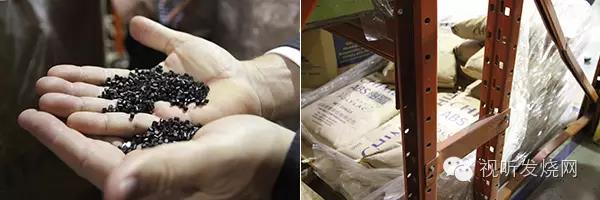 |
PVC塑料粒,是向台湾奇美采购的原材料。 |
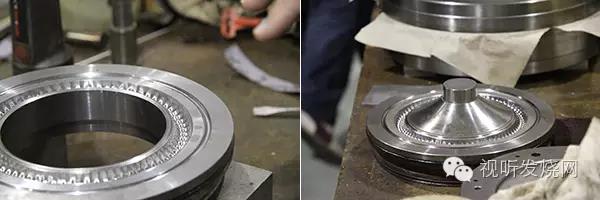 |
压制振膜的模具。 |
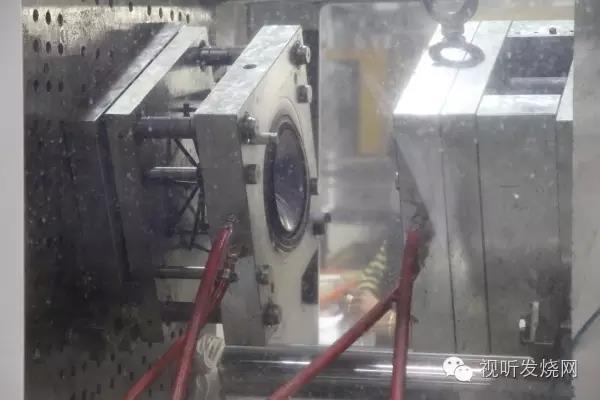 |
制作中的喇叭振膜与悬边。 |
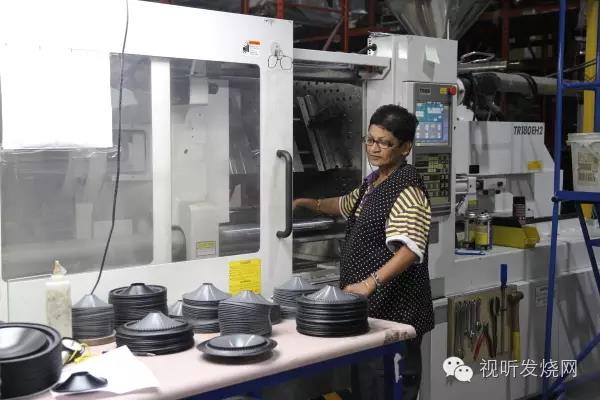 |
工作人员正在操作机器,制作喇叭振膜。 |
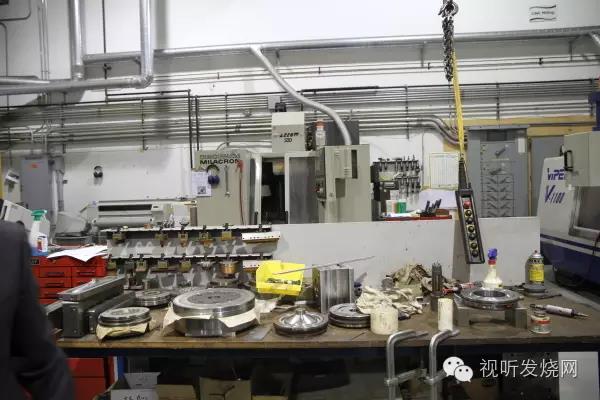 |
这是制作中音单元振膜的机器,工作台上有各种尺寸的模具。 |
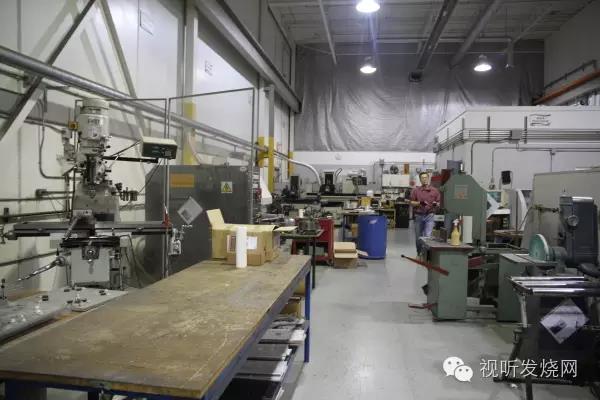 |
这里是「金工区」,Paradigm连开模都在自家工厂里面制作。 |
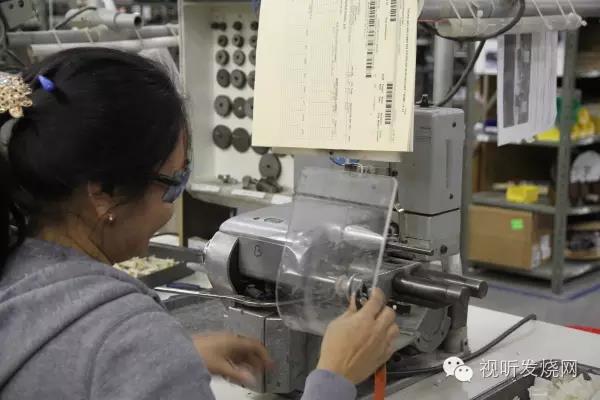 |
工作人员正在绕制电感,这是分音器的重要零件,Paradigm也要自己做。 |
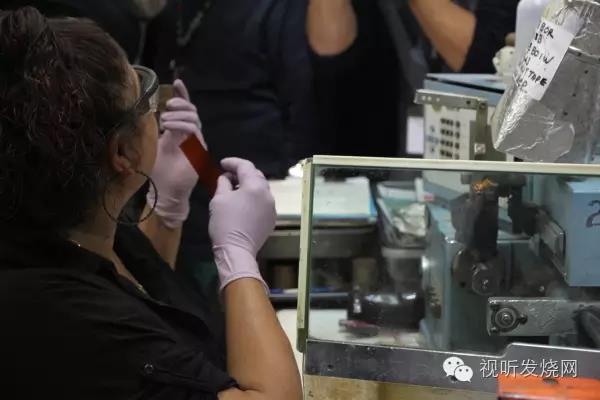 |
喇叭音圈当然要自己绕,工作人员正在准备音圈套筒,准备上机绕线。 |
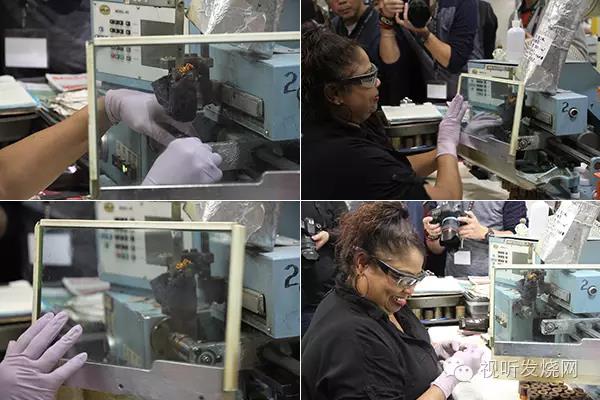 |
套上音圈套筒,接好线,开机自动绕,这样就音圈就初步完成了。 |
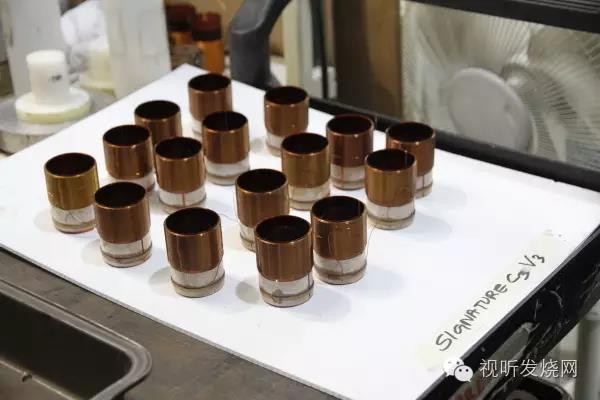 |
从音圈成品的工作平台上看,是Signature系列所使用的零件。 |
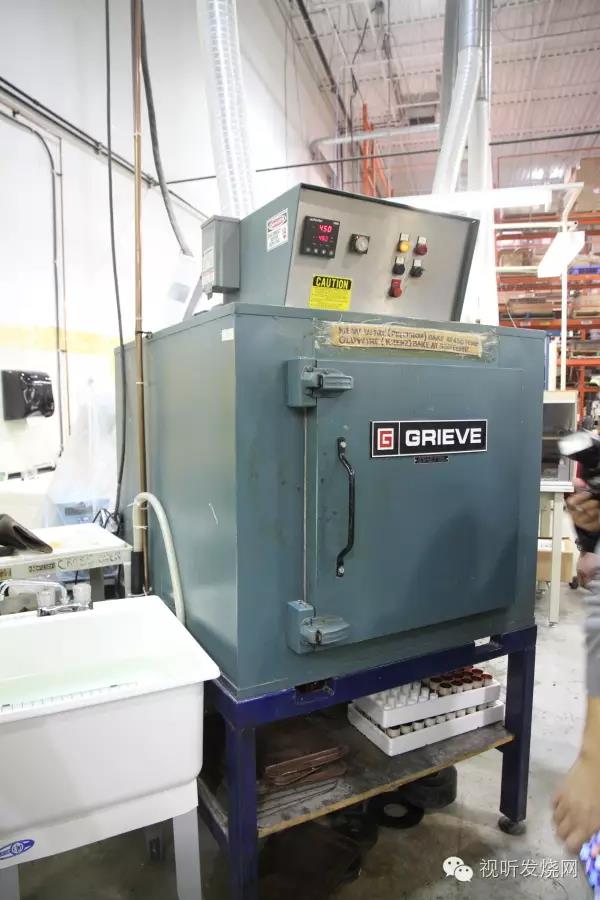 |
绕好的音圈还要送入烤箱,这样才能完全定型,日后单元就不怕您操。1吋高音要用450度烤20分钟,1.5吋用360度烤20分钟。 |
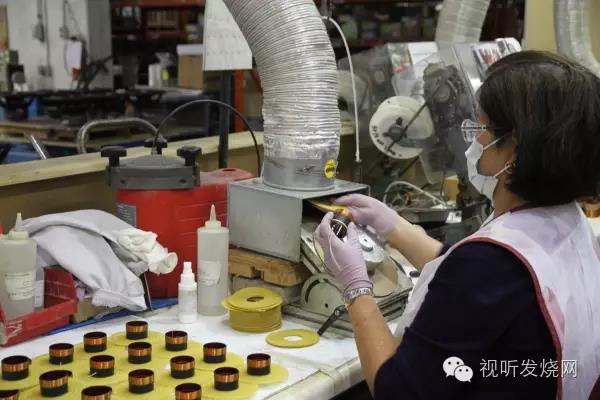 |
组合音圈与弹波。 |
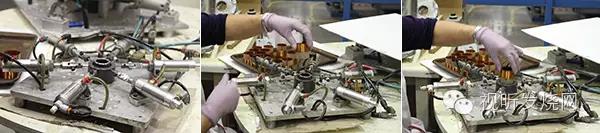 |
这是什么?怎么像六箭穿心?这是要在音圈周围挖洞,提升音圈的散热效率。 |
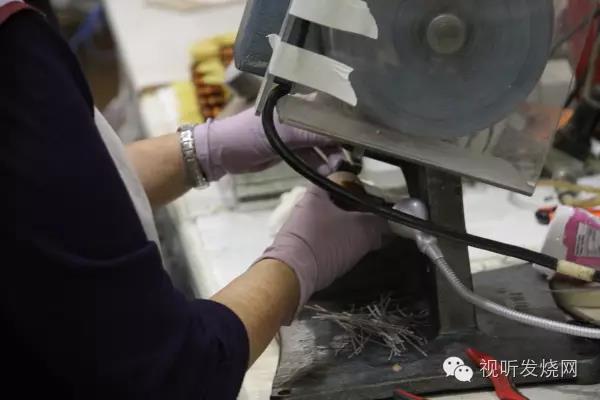 |
为音圈焊上两条导线,这样才能通电。 |
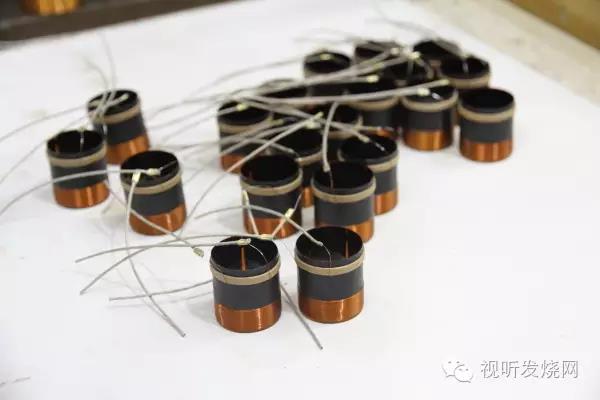 |
装上导线的音圈成品。 |
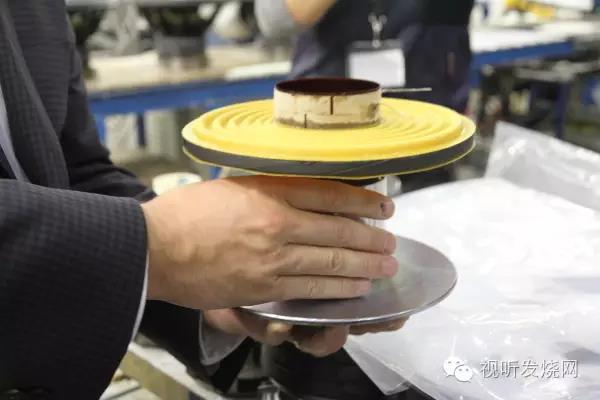 |
与弹波结合的音圈,要靠制具对准中心。 |
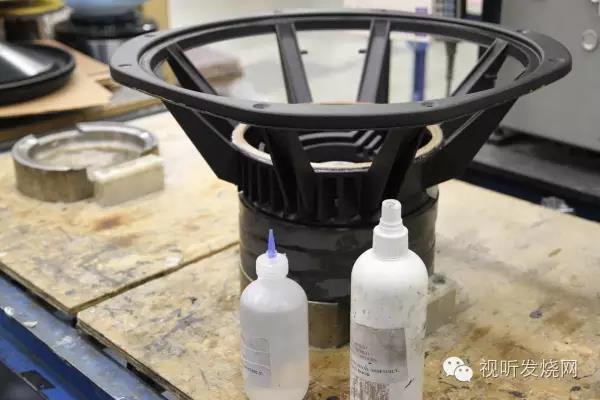 |
准备组装的超低音单元,15吋喇叭框体看起来好雄壮。 |
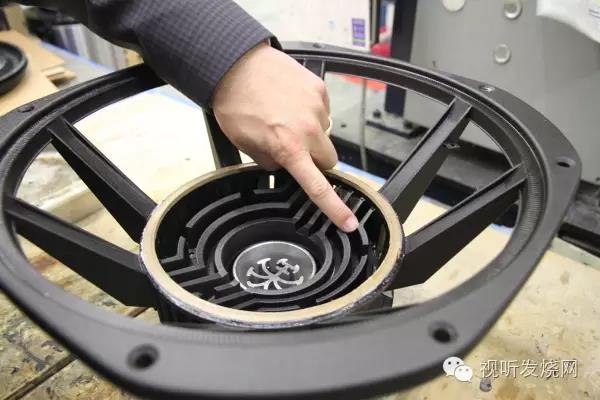 |
超低音工作时会发出高热,所以框体采用金属材料,而且内部设计了特殊形状,用来增加散热面积、提升散热效率。 |
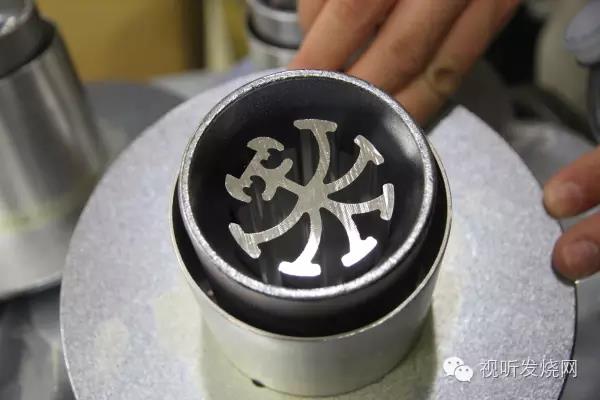 |
15吋单元中央的管子,内部还有有特殊的形状,这都是为了强化散热效果。 |
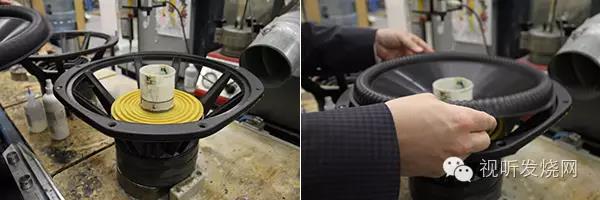 |
弹波与音圈先上,然后装上振膜与悬边,当然,中间需要胶水黏合。 |
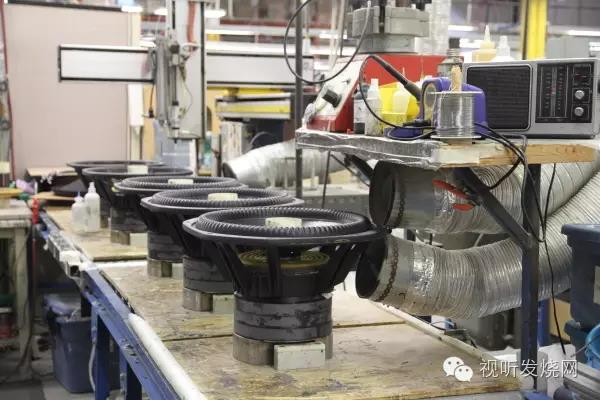 |
组装好的超低音单元,还要等待胶水凝固定型。 |
行文至此,我们大致看过Paradigm如何在自家制作喇叭单元,其中比较特殊的地方是振膜从材料开始加工,我很少看到。此外就是Paradigm的产品样式繁多,模具制作的数量也非常多,所以Paradigm干脆自己制作模具与制具,要如此深化产业垂直整合,成本相当可观,可是对Paradigm来说,这反而是降低成本的方法,靠快速研发与生产整合,在同一个工厂里提升工作效率,靠资本投入提高效率,以强化Paradigm的产品竞争力。
看过Paradigm如何在自家工厂制作单元,下一篇我们要看Paradigm如何制作音箱与分音器。

掌资讯 览精彩
关注 BrightenHiFi
将您喜欢的资讯分享
www.brightenhifi.com
info@brightenhifi.com
QQ 1341204906